Finite Element Analysis
Finite Element Analysis (FEA) is a fundamental part of the model design phase and an essential tool that has been used extensively to ensure components will be structurally sound when under load within the wind-tunnel. Whether a model design is being tested at ARA or another facility is irrelevant, all test hardware will be subject to meeting specific structural performance and safety requirements.
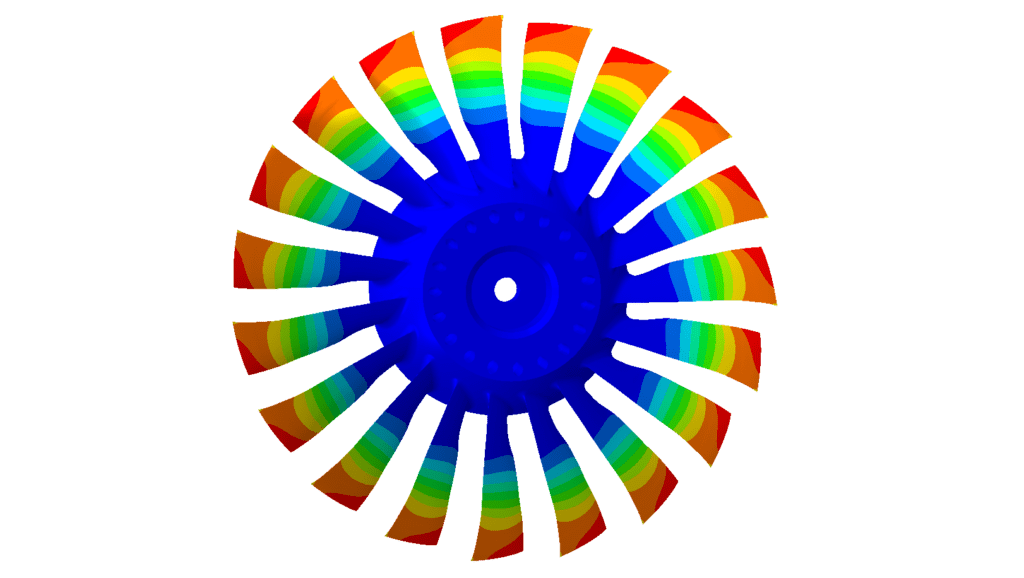
Design Engineers at ARA are experienced in the use of FEA (through CATIA’s in-built FEA package) to ensure their designs meet the required safety factors. However, sometimes advanced cost- and time-effective FEA is performed to solve various types of engineering analysis problems so the list below gives a full list of the typical analyses that are performed depending on the needs of the project:
- Structural analysis (stress, strain and linear/non-linear static)
- Thermal analysis (conduction, convection and radiation)
- Dynamic analysis (frequency, vibration, transient dynamic and contact)
- Multiphysics analysis (thermal-stress coupling, fluid-structure coupling)
ARA has committed to high standards of FEA analysis and, to this end, they have invested in licenses and training which has led to their engineers having an expertise with a number of cutting-edge commercial software packages:
- CATIA FEA
- Abaqus FEA
- Ansys Mechanical
When a model is to be tested in a facility outside of ARA, documentation relevant to the facility will be studied and a detailed stress report issued. This ensures that the model is fully compliant with the external facility’s requirements.
ARA has developed a powerful combination between the numerical and the experimental methods for a detailed structural performance insight: use of FEA to assist in the design of experiments on one hand and use of the experimental model deformation measurement techniques in the wind tunnel to support the FEA validation on the other.